Automotive Air Conditioning System
Introduction about automotive air conditioning :
Hardware Tool
1) Evaporator
2) Motor
3) Speed Meter
4) Power Supply
5) Compresser
6) Condenser
7) Control Panel Box
8) Refrigerant flow meter
9) Thermo meter
10) Variable AC motor Drives
Today, as we drive our automobiles, a great many of us, can enjoy the same comfort levels that we are accustomed to at home and at work. With the push of a button or the slide of a lever, we make the seamless transition from heating to cooling and back again without ever wondering how this change occurs. That is, unless something goes awry.
Since the advent of the automotive air conditioning system in the 1940's, many things have undergone extensive change. Improvements, such as computerized automatic temperature control (which allow you to set the desired temperature and have the system adjust automatically) and improvements to overall durability, have added complexity to today's modern air conditioning system. Unfortunately, the days of "do-it-yourself" repair to these systems, is almost a thing of the past.
To add to the complications, we now have tough environmental regulations that govern the very simplest of tasks, such as recharging the system with refrigerant R12 commonly referred to as Freon® (Freon is the trade name for the refrigerant R-12, that was manufactured by DuPont). Extensive scientific studies have proven the damaging effects of this refrigerant to our ozone layer, and its manufacture has been banned by the U.S. and many other countries that have joined together to sign the Montreal Protocol, a landmark agreement that was introduced in the 1980's to limit the production and use of chemicals known to deplete the ozone layer.
Now more than ever, your auto mechanic is at the mercy of this new environmental legislation. Not only is he required to be certified to purchase refrigerant and repair your air conditioner, his shop must also incur the cost of purchasing expensive dedicated equipment that insures the capture of these ozone depleting chemicals, should the system be opened up for repair. Simply put, if your mechanic has to spend more to repair your vehicle - he will have to charge you more. Basic knowledge of your air conditioning system is important, as this will allow you to make a more informed decision on your repair options.
Should a major problem arise from your air conditioner, you may encounter new terminology. Words like "retrofit" and "alternative refrigerant" are now in your mechanics glossary. You may be given an option of "retrofitting", as opposed to merely repairing and recharging with Freon. Retrofitting involves making the necessary changes to your system, which will allow it to use the new industry accepted, "environmentally friendly" refrigerant, R-134a. This new refrigerant has a higher operating pressure, therefore, your system, dependant on age, may require larger or more robust parts to counter its inherent high pressure characteristics. This, in some cases, will add significantly to the final cost of the repair. And if not performed properly, may reduce cooling efficiency which equates to higher operating costs and reduced comfort.
Vehicles are found to have primarily three different types of air conditioning systems. While each of the three types differ, the concept and design are very similar to one another. The most common components which make up these automotive systems are the following:
COMPRESSOR, CONDENSER, EVAPORATOR, ORIFICE TUBE, THERMAL EXPANSION VALVE , RECEIVER-DRIER,ACCUMULATOR. Note: if your car has an Orifice tube, it will not have a Thermal Expansion Valve as these two devices serve the same purpose. Also, you will either have a Receiver-Dryer or an Accumulator, but not both.
JURUTERA MEKANIKAL ISLAM-IBNU ISMAIL AL JAZARI
KINCIR air atau noria di Fayyoum, Mesir, adalah sebahagian kecil pembaharuan yang berlaku pada zaman kegemilangan empayar Islam yang menjana pertumbuhan penduduk di kawasan pedalaman daripada tradisi nomad kepada penempatan tetap.
Di bawah empayar Islam, perkembangan sistem saliran diperbaiki sehingga tidak lagi bergantung kepada tenaga manusia atau haiwan.
Mekanisme kejuruteraan inilah melahirkan istilah baru, ‘automata’ atau automatik yang bermakna berjalan dengan sendiri oleh tabii alam.
Menerusi mekanisma itu, penggunaan air dibentuk dalam dwifungsi, arus air menjadi penolak alat takungan ke kedudukan atas berulang kali dengan bantuan graviti, sambil saliran air disalurkan untuk keperluan diri dan tanaman.
Ilmu pengetahuan dan ciptaan kincir air yang kemudiannya memberi inspirasi kepada bidang kejuruteraan moden ini adalah hasil kepakaran tokoh terkenal, Al-Jazari atau nama sebenarnya Badi Al-Zaman Abullezz Ibn Alrazz Al-Jazari.
Beliau digelar Al-Jazari mengambil sempena nama tempat kelahirannya di Al-Jazira, sebuah wilayah yang terletak di antara Tigris dan Efrat, Iraq.
Kegemilangan Al-Jazari adalah hasil manuskrip beliau berjudul ‘Kitab fi ma’rifat al-hiyal al-handasiyya’ yang bermaksud ‘buku mengenai ilmu alat mekanikal yang bijak’.
Manuskrip itu menjadi bukti catatan terawal penggunaan engkol, piston dan injap yang digunakan untuk menghasilkan produk yang menjadi kegunaan harian masyarakat pada waktu itu seperti mesin pengepam air.
Sememangnya masyarakat dulu memang sudah lama memanfaatkan peralatan untuk mendapatkan air menggunakan shaduf, alat yang terdiri daripada blok panjang diletakkan antara dua tiang dengan blok kayu mendatar.
Peralatan lain ialah saqiya, di mana mekanisma tengahnya terdiri dari dua gigi dan mesin itu menggunakan tenaga haiwan seperti unta atau keldai.
Ilmuwan Muslim melakukan penyelidikan mengenai peralatan berkenaan untuk mendapatkan hasil lebih memuaskan termasuk Al-Jazari yang merintis jalan menghasilkan mesin mengepam air.
Dua mesin pertama ciptaannya adalah hasil pengubahsuaian shaduf dan yang ketiga saqiya di mana tenaga air digunakan menggantikan tenaga binatang.
Mesin yang sama seperti saqiya di letakkan di sungai Yazid di Damsyik bagi kegunaan rumah sakit yang terletak berdekatan sungai itu.
Hasil ciptaannya kelima ialah mesin yang menggunakan engkol, alat yang menghasilkan gerakan berterusan dan penemuan itu berjaya mencipta sejarah kerana engkol adalah peralatan mekanik paling penting bagi orang Eropah awal abad ke-15.
Al-Jazari mengembangkan mesin engkol yang dihubungkan dengan sistem rod pada mesin pengepam air dan ini dilakukan beliau pada 1206.
Beliau juga menghasilkan mesin yang digerakkan oleh air bagi menggerakkan piston yang saling berhubungan dengan paip penyedut pada dan ia adalah contoh prinsip double acting yang pertama.
Al Jazari kemudian mengumpulkan semua hasil karyanya berkaitan bidang teknikal yang lengkap dengan maklumat dari segi teori dan praktikal dalam buku berjudul Al-Jami Baim Al-Ilm wal Amal Al-Nafi Fi Sinat’at Al Hiyal.
Berkat kemampuan mekaniknya, al-Jazari tercatat mampu merakit beberapa jenis jam air. “Salah satunya, sebuah jam dengan tenaga air yang tingginya satu meter dan lebarnya satu setengah meter. Jam itu berhasil direkonstruksi di Museum Ilmu Pengetahuan tahun 1976,” ungkap Donald Routledge Hill dalam karyanya A History of Engineering in Classical and Medieval Times.
Al-Jazari juga mampu membuat jam air berbentuk gajah. Bahkan, jam buatan al-Jazari sudah mampu menghasilkan suara. Dalam manuskrip al-Jazari, jam itu merupakan jam terawal yang menggunakan flow regulator, sebuah sistem tutup-lubang dan sebuah otomaton seperti sebuah jam burung.
“Jam ini merupakan jam pertama dengan reaksi otomatis dalam interval waktu. Jam ini menggunakan sebuah robot manusia (humanoid) yang membentur gembreng dan sebuah robot burung mekanik secara otomatis bersiul. Jam air ini juga dikenal sebagai jam pertama yang bisa merekam waktu secara akurat untuk menyesuaikan lamanya hari yang tidak sama sepanjang tahun,” imbuh al-Hassan dan Hill.
Rancangan jam air buatan al-Jazari juga diakui sangat bagus. ”Jam al-Jazari penuh dengan ide-ide dan teknik-teknik yang penting bagi sejarah perancangan mesin,” kata al-Hassan dan Hill.
Karyanya berbeza dengan karya ilmuwan lain kerana beliau memberi penerangan terperinci mengenai ilmu mekanikal yang mengandungi 50 peralatan yang dibahagikan kepada enam kategori.
Antaranya, jam air, alat mencuci tangan dan mesin pengepam air. Jam air adalah hasil kerja gemilang Al-Jazari yang dikagumi pada acara World of Islam Festival pada 1976.
Karya beliau juga dianggap sebagai sebuah manuskrip terkenal di dunia dan menjadi teks penting untuk mempelajari sejarah teknologi kerana dilengkapi ilustrasi menakjubkan.
Dengan karya gemilangnya, ilmuwan dan jurutera Islam yang mengabadikan diri di istana Artuqid di bawah naungan Sultan Nasir al-Din Mahmoud telah membawa masyarakat Islam pada abad ke-12 kepada kejayaan.
Jurutera Inggeris, Donald Hill yang tertarik dengan karya Al-Jazari menterjemahkan bukunya pada 1974.
Pendekatan Al-Jazari yang menjadi asas kepada perkembangan teknologi industri pada abad ke-18, diakui pakar tempatan, pensyarah dan juga penyelidik Fakulti Kejuruteraan Universiti Kebangsaan Malaysia (UKM), Prof Dr Wan Ramli Wan Daud.
Beliau bersama kumpulannya berjaya mencipta enjin menggunakan tenaga sel kimia berkuasa 200 watt bagi menggerakkan motosikal.
Menurut Wan Ramli, apa yang diperlukan sekarang ialah menyuntik semula semangat yang dijelmakan oleh ilmuwan seperti Al-Jazari, dengan menghasilkan ciptaan untuk kesejahteraan sejagat.
What your understand about Lathe Machine?
OBJEKTIF AM
Dapat mengetahui jenis-jenis mesin larik dan mata alat serta berkebolehan mengendalikan mesin larik.
OBJEKTIF KHUSUS
Di akhir unit ini anda sepatutnya dapat :
Mengenali jenis-jenis mesin larik.
Mengetahui fungsi bahagian-bahagian mesin larik tetengah.
Mengetahui kaedah bagaimana benda kerja dipegang pada mesin larik.
Memahami fungsi dan jenis-jenis mata alat.
Mengetahui sudut-sudut yang ada pada mata alat.
Mengetahui jenis bahan dan kegunaan mata alat.
Mengetahui langkah pengendalian kerja-kerja menggerek, menggerudi, melorek, melarik tirus, memotong ulir skru dan melarik tak sepusat.
6.0 PENGENALAN
Mesin larik ialah satu-satunya mesin yang paling versatil dalam bengkel kejuruteraan. Walaupun pelbagai betuk mesin pelarik telah digunakan sebelum kurun ke-18, nanun mesin pelarik pertama yang boleh memotong ulir hanya dicipta pada tahun 1797 oleh seorang mekanik Inggeris bernama Henry Maudslay. Mesin ciptaan beliau telah banyak digunakan dalam pembinaan enjin stim kereta api rekaan James Watt pada awal kurun ke-19 iaitu pada zaman revolusi industri England.sejak dari masa itu mesin ini telah diperbaiki dan ditambah dengan beberapa alatan tambahan supaya dapat mengeluarkan komponen-komponen dengan tepat dan persis. Di Malaysia mesin ini amat popular sehingga setiap bengkel kejuruteraan mempunyai sekurang-kurangnya sebuah mesin.
JENIS-JENIS MESIN LARIK
Mesin pelarik boleh dijumpai dalam beberapa bentuk dan saiz. Jenis yang terkecil digunakan dalam pengeluaran komponen kecil jam tangan sementara yang besar sekali digunakan untuk memesin syaf berat. Mesin pelarik boleh dikelaskan kepada dua kategori :
Mesin Pelarik Jentera
Dalam kategori ini terdapat empat jenis mesin pelarik.
1) Jenis bangku
Mesin ini kecil dan boleh dipasang diatas bangku atau kabinet besi. Ia digunakan untuk menghasilkan kerja yang ringan dan halus.
2) Mesin pelarik piawai (mesin larik tetengah)
Mesin ini lebih besar dan berat daripada jenis bangku. Panjang landasan mesin adalah 1.5 meter hingga 6 meter. Lazimnya mesin ini digunakan untuk kerja-kerja penyelenggaraan sederhana dan juga dalam institusi latihan kemahiran.
3) Jenis toolroom
Jenis mesin ini lebih persis dan digunakan dalam pembinaan Tool dan Die. Mesin ini juga dilengkapi dengan alat tambahan khas dan aksesori supaya beberapa operasi Tool dan Die boleh dilakukan.
4) Jenis gap-bed
Saiz mesin ini lebih besar daripada jenis bangku. Sebahagian daripada landasannya di bawah cuk boleh ditanggalkan supaya bahan kerja atau kompenen dengan diameter yang lebih besar boleh dipegang.
Jenis Mesin Pengeluaran
Ada lima jenis mesin pelarik untuk kategori ini :
(a) Pelarik turret pelana
Pelarik turret pelana juga disebut jenis mesin pelarik turret. Mesin ini mempunyai kepala turret yang dipasang pada pelana yang bergerak diatas landasan. Kepala turret boleh memegang beberapa jenis mata pemotong dan boleh digunakan untuk melarik beberapa operasi tanpa memberhentikan mesin untuk menukar mata alat.
(b) Pelarik kapstan
Pelarik kapstan juga disebut pelarik turret pelantak. Mesin ini kecil sedikit saiznya daripada jenis pelarik turret. Ia digunakan untuk melakukan kerja-kerja sederhana dan ringan sahaja. Kepala turret mesin ini terletak diatas satu kekesot berbentuk landasan pendek. Landasan pendek ini pula menggelongsor diatas landasan utama mesin dan boleh dikunci pada sebarang kedudukan yang dikehendaki.
(c) Pelarik automatik
Jenis mesin pelarik automatik dicipta untuk pengeluaran kuantiti diantara beberapa ratus sehingga beberapa puluh ribu kompenen sehari. Semua pergerakan mata pemotong dan bahan kerja dikawal oleh sesondol (cam), sistem hidraulik atau sistem elektro mekanik.
d) Pelarik kegunaan khas
Pelarik jenis ini dicipta untuk melakukan kerja-kerja khas seperti :
*pelarik roda kereta api
*pelarik aksel
*pelarik penampang
*pelarik menegak
(e) Pelarik N.C dan C.N.C
Mesin pelarik terbaru ini berfungsi dibawah kawalan komputer. Mesin ini lebih produktif dan hasil pengeluarannya lebih persis jika dibandingkan dengan mesin lain. Terdapat dua jenis mesin iaitu :
*Jenis yang mempunyai turret dipasang pada landasan mesin sahaja.
*Jenis yang mempunkyai dua turret dimana satu turret dipasang pada landasan dan satu lagi pada kekesot lintang.
FUNGSI BAHAGIAN-BAHAGIAN MESIN LARIK TETENGAH
Bahagian-bahagian utama mesin pelarik terdiri daripada landasan, alatan hadapan, alatan belakang, kekotak gear cepat tukar dan kereta.
1) Landasan
(a) Landasan adalah tulang belakang sebuah mesin pelarik. Kejituan mesin pelarik bergantung pada ketegaran, penjajaran dan ketepatan pada landasannya.
(b) Bahagian atas landasan boleh berbentuk ‘V’ atau rata dan diatasnya terletak peralatan lain seperti alatan hadapan, kereta dan alatan hadapan.
(c) Landasan diperbuat daripada besi tuangan yang bermutu tinggi. Rawatan haba kekerasan dilakukan keatasnya supaya boleh tahan haus.
2) Alatan hadapan
(a) Bahagian ini terletak di sebelah kiri landasan mesin.
(b) Spindal utama yang berbentuk satu syaf geronggang yang disokong oleh beberapa galas terletak di dalam bahagian ini. Hujunjg spindal atau muncungnya yang terkeluar daripada alatan hadapan yang berbentuk jenis tirus, jenis ulir atau jenis kekunci sesondol ( kam lock )
(c) Pada hujung spindal ini beberapa peraltan seperti cuk, piring pelarik dan tetengah hidup boleh dipasang dan digunakan untk memegang bahan kerja atau kompenen yang hendak dilarik.
(d) Untuk memutarkan spindal utama, alatan hadapan mempunyai perlatan takal atau beberapa siri rangkaian gear. Alatan hadapan bergear mempunyai lebih rangkaian kelajuan dan lebih tepat putarannya jika dibandingkan dengan alatan hadapan yang bertakal. Lagipun takal boleh tergelincir bila terkena minyak dan ini menyebabkan hasil larikan yang tidak rata atau licin.
3 Alatan Belakang
(a) Bahagian ini terletak disebelah kanan landasan. Ia boleh digerakan disepanjang landasan dan juga boleh dikunci pada mana-mana kedudukan yang dikehendaki. Alatan belakang terdiri daripada dua bahagian utama, badan dan tapak.
(b) Pada badan terdapat satu spindal yang mempunyai penirusan piawaian Morse. Alat pemotong bertangkai tirus Morse, seperti gerudi dan pelulas boleh dipasang pada spindal tersebut.
(c) Tapak alatan belakang dimesin dengan jitu supaya boleh didudukan diatas landasan dengan tepat. Pada tapak terdapat dua skru penyelaras yang diguna untuk menjajarkan keselarian diantara tetengah mati dan tetengah hidup atau mengofsetkan alatan belakang supaya dapat melarik tuirus dengan kaedh ini.
4) Kotak gear cepat tukar
(a) Kotak gear terletak disebelah kiri landasan dan dibawah alatan hadapan. Kotak ini mempunyai beberapa gear berbilang saiz untuk memutarkan skru pemandu atau aci penghantar.
b) Skru pemandu digunakan untuk memajukan kereta semasa memotong ulir. Aci penghantar pula digunakan semasa membuat kadar penghantaran yang tertentu secara otomatik.
5) Kereta
(a) Sela
Bahagian ini ialah tuangan berbentuk huruf H dan boleh bergerak diatas landasan. Apron dan kekesot lintang dipasang pada sela.
(b)
Apron
Bahagian apron dipasang dihadapan sela dengan bolt. Apron mempunyai beberapa gear dan peralatan yang digunakan untuk mengawal pergerakan sela dan kekesot lintang. Satu tuas tangan yang dipasang dengan pinan jejaring dengan rak terletak dibawah landasan. Tuas tangan ini diputarkan apabila hendak menggerakkan kereta secara insani ( manual ). Keseluruhan bahagian kereta dan kekesott lintan boleh digerakkan secara otomatik atau insani
(c) Kekesot Lintang
Tiang mata alat dipasang pada kekesot bergabung. Kekesot bergabung pula dipasang diatas kekesot lintang dengan dua bolt. Apabila kedua-dua bolt ini dilonggarkan kekesot bergbung boleh dikilaskan pada sudut yang dikehendaki. Dengan cara ini penirusan tajam tetapi pendek boleh dilarik. Pada hujung kekesot lintang dan kekesot bergabung dilengkapi dengan relang yang ditanda jitu supaya kedalaman pemotongan dapat dilaraskan dengan tepat.
KAEDAH MEMEGANG BAHAN KERJA DI MESIN LARIK
Kaedah memegang bahan kerja dengan bindu
Jenis-jenis muncung spindal
Terdapat tiga jenis muncung spindal yang biasa terdapat pada mesin pelarik. Aksesori seperti pelbagai jenis cuk dan piring pelarik dipasang pada muncung ini. Tiga jenis muncung spindal adalah :
(1) Jenis berulir
Muncung spindal jenis berulir biasanya terdapat pada mesin-mesin kecil dan yang lama. Ulir yang terdapat pada muncung ini biasanya dari jenis bentuk ‘V’. Satu plat penyesuai yang mempunyai ulir dalam dan bentuk yang sama, dipasang pada belakang cuk. Semasa memmasang cuk ini pada muncung spindal dua perkara yang perlu diperhatikan ialah :
(a) Ulir luar dan dalam mestilah bersih. Kalau tidak pemasangan akan menjadi tidak tepat.
(b) Ulir luar pada muncung spindal tidak rosak atau sumbing, kerana ini akan menyebabkan cuk tidak boleh dipasang.
(2) Jenis tirus Amerika
Muncung spindal ini bertirus piawai Amerika iaitu 89 mm untuk setiap 305 mm (3.5 inci untuk setiap kaki). Tirus ini tajam dan membolehkan aksesori seperti cuk dan pirin pelarik dibersih dan dipasang atau ditanggal dengan pantas. Satu kekunci pada muncung tirusdigunakan untuk menempatkan cuk atau piring pelarik pada kedudukan yang tepat. Gelang kekunci yang berulir itu pula digunakan untuk mengikat cuk pada spindal utama mesin.
(3) jenis Kam-Lock
Permukaan muncung spindal ini mempunyai tiga atau enam lubang telusan. Fungsi lubang ini adalah untuk menempatkan dan mengunci stad kekunci sesondol yang ada pada aksesori yang perlu dipasang. Separa putaran kam-lock akan melepaskan stad ini dan membolehkan aksesori itu dikeluarkan dengan mudah dan cepat. Dari segi penggunaan, jenis kam-lock adalah cepat jika dibandingkan dengan yang lain.
Rajah dibawah menunjukkan tiga kaedah digunakan untuk memegang bahan kerja dengan cuk tiga rahang. Walaubagaimanapun berhati-hatilah semasa menggunakan kaedah seperti ditunjukkan dalam rajah (a) dan (c) kerana kaedah ini bahan kerja munngkin tergelincir keluar jika hantaran dan kedalaman pemotongan berlebihan dilakukan. Bahan kerja bulat dan berbentuk heksagon boleh dipegang dengan cuk tiga rahang.
Kaedah memegang bahan kerja dengan cuk empat rahang
Rajah dibawah menunjukan tiga kaedah yang digunakan untuk memegang bahan kerja dengan cuk empat rahang. Bahan kerja boleh dipegang dengan lebih persis dengan cuk jenis ini dari cuk tiga rahang. Pemusatan bahan kerja secara kasar boleh dilakukan dengan bantuan lengkung sepusat yang ada pada muka cuk. Dua cara yang lebih persis adalah dengan bantuan tolok permukaan dan tolok dail.
Kaedah memegang bahan kerja dengan cuk kolet
Rajah dibawah menunjukkan kaedah memegang bahn kerja dengan cuk kolet jenis ‘draw back’. Cuk kolet ini biasanya digunakan untuk memegang dan memesin komponen-komponen yang kecil dengan cepat dan tepat. Untuk mengunci, bar penarik diputarkan dan ini menyebabkan kolet ditarik ke dalam sarung tirus. Proses ini membolehkan kolet mencengkam bahan kerja dengan lebih jitu dan tepat.
Kedah memegang dengan sangga tetap
Rajah dibawah menunjukkan kaedah memegang bahan kerja dengan sangga tetap. Aksesori ini palingsesuai sekali digunakan untuk menyokong bahan kerja yang panjang dan yang perlu dimesin pada hujungnya. Biasanya bahan kerja yang ukuran panjangnya 3 kali ganda diameter perlu disokong oleh sangga atau tetengah untuk mengelak bahan kerja dari bengkok atau memegas (spring).
Kaedah memegang dengan sangga bergerak
Rajah dibawah menunjukkan kaedah penggunaan sangga bergerak semasa melarik bahan kerja yang panjang. Sanggabergerak mengelakkan bahan kerja memegas pada kedudukan mata alat semasa proses memesin sedang dijalankan. Amat sesuai digunakan semasa melarik selari pada bahan kerja yang berdiameter kecil dan panjang.
Lelabah
Rajah dibawah menunjukkan sebuah lelabah (spider) dan penggunaannya. Lelabah biasanya digunakan untuk menyokong paip atau tiub yang panjang. Satu hujung dipegang pada cuk tiga rahang dan satu lagi dipasang dengan lelabah. Pada pusat lelabah terdapat lubang tetengah dimana tetengah dipasangkan.
Kepala kekucing
Rajah dibawah menunjukkan kepala kekucing. Alat ini perlu digunakan bersama
dengan sangga tetap. Kepala kekucing berfungsi sebagai penyokong dan
pengalas untuk syaf yang panjang. Syaf ini mungkin telah dimesin dengan jitu
dan licin. Dengan penggunaan kepala kekucing permukaan syaf boleh dielak dari
tercalar semasa melarik. Syaf panjang yang berbentuk heksagon juga boleh
dipasang dengan kepala kekucing supaya dapat disangga dengan mudah.
MEMAHAMI FUNGSI DAN JENIS-JENIS MATA ALAT
Faktor yang menentukan kecekapan sebuah mesin larik ialah bentuk dan jenis mata alat yang digunakan. Bahan mata alat yang digunakan haruslah memepunyai sifat-sifat berikut:
(a) Bahan mestilah keras
(b) Mempunyai rintangan kehausan
(c) Menahan sifat kekerasan pada suhu yang tinggi semasa memotong
(d) Menyerap kejutan semasa melakukan operasi seperti melarik eksentrik dan larikan kasar.
Diantara jenis-jenis mata alat yang biasa digunakan bagi kerja-kerja melarik biasa ialah :
a. Mata alat pemotongan biasa
b. Mata alat melurah
c. Mata alat membenang
-Jenis ‘V’
-Jenis Acme
-Jenis Buttres
-Jenis Bersegi
d. Mata alat jenis sisip (Throwaway)
e. Mata alat menggerek dan sebagainya
SUDUT-SUDUT YANG ADA PADA MATA ALAT
SUDUT SADAK ATAS (top rake)
Fungsi utama sudut ini adalah dalam pengeluaran tatal semasa larikan dibuat. (sudut ini curam positif atau negetif, lihat rajah). Sudut ini bergantung kepada jenis bahan yang dipotong. Sudut sadak atas untuk bahan lembut seperti loyang adalah lebih besar daripada misalnya bahan keluli lembut. Untuk memesin yang terlalu keras atau lembut sudut sadak atas dicadangkan bersudut negetif.
SUDUT SADAK TEPI
Sudut ini bergantung kepada bahan yang dilarik dan jenis operasi yang dilakukan, contohnya melarik kasar, penyudahan dan sebagainya. Sudut tepi yang besar membolehkan tatal keluar dengan mudah dan mengurangkan geseran tetapi melemahkan sudut pemotongan. Sudut sadak tepi yang kecil dan negetif akan memperkuatkan sudut pemotongan tetapi ini akan menjejaskan pengeluaran tatal dan akan menambahkan bebanan keatas mata alat.
SUDUT TELUSAN HADAPAN
Sudut telusan hadapan mengelakan mata alat daripada menggesel bahan kerja yang dimesin. Saiz sudut ini bergantung pada kadar dataran dan diameter bahan kerja yang dimesin. Jika sudut ini terlalu kecil, mata alat akan menggesel bahan kerja dan tidak akan memotong dengan baik serta menghasilkan penyudahan yang kasar. Jika terlalu besar pula, poin mata alat akan menjadi lemah, mudah terbakar dan patah.
SUDUT TELUSAN TEPI
Sudut telusan tepi bergantung kepada kekerasan bahan yang dilarik dan kadar hantaran pemotongan. Untuk bahan kerja keluli sudutnya adalah antara 6 hingga 10 dan untuk bahan yang lebih keras suditnya adalah 4. sudut ini boleh dikurangkan jika berlaku gelatuk (chatter). Sebaliknya sudut ini ditambah jika berlaku getaran.
SUDUT PEMOTONG TEPI
Sudut ini adalah antara 10 hingga 25 dan bergantung kepada aplikasinya, mislnya operasi jenis melarik penampang, melarik kasar dan sebagainya. Jika sudut pemotong tepi terlalu besar ini akan menyebabkan mata alat menggelatuk.
SUDUT PEMOTONG HUJUNG
Sudut ini juga boleh berubah mengikut aplikasinya. Untuk melarik kasar suduut 5 hingga 15 digunakan. Sudut yang kecil akan memperkukuhkan hujung mata alat. Untuk melarik biasa sudutnya antara 15 hingga 30. Sudut yang besar mata alat dikilas kekiri supaya operasi melarik bahu dan larikan hampir dengan cuk boleh dilakukan.
What your understand about Gas Welding??
OBJEKTIF AM
Memahami konsep kimpalan gas serta serta kegunaannya dalam bidang perindustrian.
OBJEKTIF KHUSUS
Di akhir unit ini anda dapat :
Mendefinasikan kimpalan gas dan menerangkan perkara-perkara yang berkaitan dengannya iaitu:
Kimpalan gas tekanan tinggi dan
kimpalan gas tekanan rendah.
Kegunaan kimpalan gas dalam
industri.
Jenis-jenis gas untuk kegunaan kimpalan
gas.
Sifat gas oksigen, cara pengeluaran dan
silinder oksigen.
Sifat-sifat gas asetilina ,cara pengeluaran
dan silinder asetlina.
Jenis-jenis gas sebagai bahan bakar.
Kelengkapan kimpalan gas oksi-asetilina.
Tugas serta prinsip-prinsip alatur satu
peringkat dan dua peringkat.
Jenis-jenis hos untuk kimplan oksi-
asetilina.
Prinsip serta jenis-jenis sumpitan api.
Sistem pancarongga dan sistem stesen
tunggal kimpalan oksi-asetilina.
7.0 PENGENALAN:
‘Kimpalan Gas’ adalah satu cabang daripada kerja kimpalan yang telah lama diamalkan dalam bidang industri. Terutama sekali dalam bidang fabrikasi logam. Ini adalah kerana kimpalan gas adalah didapati amat sesuai untuk kepingan logam-logam yang nipis. Contoh bidang kerja yang melibatkan proses kimpalan gas ialah kerja membaikpulih badan kenderaan serta kerja-kerja fabrikasi logam yang melibatkan kepingan logam nipis.
Pada awal kurun kedua-puluh manusia telah mengetahui cara menyambung logam dengan memanaskan dua batang logam hingga merah menyala dan seterusnya impak yang kuat dikenakan ke atas kedua-duanya sehinggalah kedua-duanya bercantum menjadi satu. Proses ini dipanggil sebagai kimpalan tempa. Kaedah ini telah diperbaiki dari masa kesemasa seiring dengan perkembangan teknologi sehinggalah kaedah terkini kimpalan gas telah dapat kita semua gunakan sekarang ini.
7.1 Definasi Kimpalan Gas
Kimpalan gas didefinasikan sebagai satu proses penyambungan logam dengan kaedah memanaskan kedua-dua bahagian logam yang hendak disambung sehingga cair dan bercantum menjadi satu.
7.2 Kimpalan Gas Tekanan Rendah Dan Kimpalan Gas Tekanan Tinggi
7.2.1 Terdapat dua jenis kimpalan gas iaitu:
Kimpalan gas tekanan rendah
Kimpalan gas tekanan tinggi.
Kimpalan tekanan rendah menerima bekalan gas asetilina dari janakuasa gas asetilina yang mempunyai tekanan kurang dari 1.0 psi atau 1.0 Bar
Kimpalan gas tekanan tinggi menerima bekalan gas dari janakuasa gas asetilina yang mempunyai tekanan dari 1-15psi atau 1-15 Bar.
7.3 Kegunaan kimpalan gas dalam industri
Dalam bidang perindustrian kimpalan gas banyak digunakan dalam kerja fabrikasi logam yang melibatkan kepingan logam yang ketebalannya melebihi daripada 1.0mm sehingga 3.0mm. Contohnya, dalam kerja-kerja membaikpulih badan kenderaan yang melibatkan kerja-kerja ketuk mengetuk dan menampal bahagian-bahagian badan kenderaan yang rosak.
7.4 Gas
Dua jenis gas yang biasa digunakan dalam kerja kimpalan gas adalah oksigen(O ) dan asetilina (C H ). Campuran kedua-dua gas menghasilkan haba yang paling tinggi berbanding gas-gas bahanapi yang lainnya. Suhunya boleh mencapai sehingga 3316C.
7.5 Gas Oksigen
Gas oksigen tidak mempunyai warna , rasa dan bau. Ia juga merupakan sejenis gas yang dapat memebantu dalam proses pembakaran dan juga merupakan gas aktif yang boleh bertindakbalas ke atas logam yang menyebabkan pengoksidanan berlaku ke atas logam berkenaan. Contohnya, pengkaratan ke atas keluli.
7.5.1 Penghasilan Gas Oksigen
Gas oksigen boleh dihasil melalui beberapa kaedah, iaitu:
i) Kaedah penyulingan udara.(pemeringkatan udara)
ii) Kaedah elektrolisis
Kaedah penyulingan udara adalah satu kaedah yang dilakukan secara komersial. Ianya dilakukan melalui proses pengasingan oksigen daripada udara yang dipanggil proses penyulingan udara cair yang termampat pada ketekanan 206 bar (3000psi) iaitu pada suhu -160C. Seterus tekanan akan akan di kurangkan sedikit demi sedikit dimana oksigen dalam bentuk cair akan bertukar menjadi gas lalu ditabungkan. Begitulah bagi gas-gas yang lainnya akan bertukar menjadi gas apabila tekanan dikurangkan dan ditabungkan untuk kegunaan yang lain.
Kaedah elektrolisis adalah satu proses penghasilan gas oksigen yang diperolehi melalui arus elektrik di dalam air. Proses ini sangat mahal dan tidak ekonomi untuk dikomersialkan.
Gas oksigen akan disimpan dalam silinder keluli yang berwarna hitam dan
lebih tinggi daripada silinder asetilina. Ianya tidak bersambung dan berupaya menahan tekanan setinggi 3360 psi. Boleh didapati dalam tiga saiz.
Contoh 7.1
Apakah perbezaan antara kimpal an tekanan tinggi dan kimpalan tekanan rendah?
Penyelesaian:
- Kimpalan tekanan rendah menerima bekalan gas asetilina dari janakuasa gas asetilina yang mempunyai tekanan kurang dari 1.0 psi atau 1.0 Bar
- Kimpalan tekanan rendah menggunakan badan sumpitan
jenis ‘injector’
- Kimpalan gas tekanan tinggi menerima bekalan gas dari janakuasa gas asetilina yang mempunyai tekanan dari 1-15psi atau 1-15 Bar.
- Menggunakan badan sumpitan api jenis tekanan seimbang
7.6 Jenis-Jenis Gas Bahan Bakar
7.6.1 Gas Asetilina:
Gas asetilina adalah bahanapi yang tidak mempunyai warna tetapi mempunyai bau yang kuat dan mudah terbakar .Ia adalah gas yang tidak stabil dan perlu disimpan dalam keadaan yang tetap. Titik kritikal bagi gas asetilina ialah pada tekanan 28 psi pada suhu 70F.
Penghasilan gas asetilina:
Gas asetilina dapat dihasilkan dengan mencampurkan kalsium karbida dan air. Terdapat dua jenis janakuasa yang menghasikan gas asetilina, iaitu:
i) janakuasa tekanan rendah .
ii) janakuasa tekanan tinggi
Gas asetilina disimpan dalam silinder keluli berwarna maroon yang diisikan dengan bahan berliang sepenuhnya yang terdiri daripada habuk kayu balsa, arang kayu,simen,dan bahan-bahan telap yang lain.
Bahan-bahan telap yang dimuatkan ke dalam silinder asetilina adalah berfungsi untuk menyerap seberapa banyak cairan aseton. Aseton ini pula akan berfungsi untuk menyerap gas asetilana sebanyak 25 kali ganda isipadunya sendiri.
Contoh 7.2
Namakan dua jenis janakuasa dalam penghasilan gas asetilina.
Penyelesaian:
Dua jenis janakuasa gas asetilina ialah:
- Janakuasa tekanan tinggi (karbida kepada air – melebihi 20 meter padu )
- Janakuasa tekanan rendah.( air kepada karbida – kurang dari 20 meter padu )
7.6.2 Gas Bahanapi Yang Lain-Lain
Selain daripada asetilina terdapat juga gas-gas bahanapi yang lain yang mana campuran gas ini bersama oksigen akan menghasilkan suhu yang agak tinggi. Berikut adalah perbandingan suhu-suhu bagi campuran antara dua gas.
i) oksi-asetilina 3100C - 3500C
ii) udara-asetilina 2300C - 2500C
iii) oksi-hidrogen 2200C - 2382C
1v) oksi-gas arang batu 1982C - 2182C
7.7 Kelengkapan Kimpalan Gas
7.8 Tugas Serta Prinsip-Prinsip Alatur Satu Peringkat Dan Dua Peringkat
Adalah merupakan alat kawalan yang dipasang pada bahagian atas silinder oksigen atau asetilina bagi mengawal pengaliran gas yang diperlukan untuk tujuan mengimpal dan juga untuk menunjukkan tekanan gas dalam silinder. Ianya dikenali juga dengan tolok tekanan. Terdapat dua jenis alatur iaitu alator alatur satu peringkat dan dua peringkat.
Alator juga mempunyai rekabentuk dan jenama yang berbagai. Terdapat juga alator yang mempunyai satu tolok bacaan tetapi itu tidak menunjukkan bahawa ianya jenis satu peringkat. Walau bagaimana pun alator dua peringkat mempunyai dua tolok bacaan.
Terdapat dua jenis alator yang boleh digunaka dalam pemasangan oksi-
asetilina. Iaitu:
-Alator satu peringkat
-Alator dua peringkat
7.8.1 Tugas-tugas dan fungsi alator alator.
Alator satu peringkat mempunyai satu ruang tekanan tinggi dimana tekanan tinggi dari silinder terus masuk ke dalam ruang ini bacaan tekanan dapat dilihat pada jarum alator dan sedia dikurangkan kepada tekanan untuk kerja mengikut pelarasan yang sesuai dengan menggunakan skru pelaras pad alator. Tahap keselamatan alator ini adalah rendah berbanding alator dua peringkat.
Alator dua peringkat mempunyai dua ruang tekanan iaitu ruang tekanan rendah dan ruang tekanan tinggi. Ruang tekanan tinggi pada alator menerima terus tekanan tinggi dalam silinder dan bacaan bagi tekanan ini dapat dibaca pada tolok tekanan. Manakala ruang tekanan rendah menerima gas yang dikawal kemasukannya dari ruang tekanan tinggi dengan melaraskan skru pelaras pada alator mengikut tekanan kerja yang dikehendaki. Oleh itu tahap keselamatannya adalah lebih baik berbanding alator satu peringkat.
Contoh 7.3
Senaraikan campuran gas bahan bakar dan suhu kepanasanya.
Penyelesaian:
i) oksi-asetilina 3100C - 3500C
ii) udara-asetilina 2300C - 2500C
iii) oksi-hidrogen 2200C - 2382C
1v) oksi-gas arang batu 1982C - 2182C
7.9 Jenis-Jenis Hos
Hos adalah tiub getah berlapiskan benang nylon yang kuat . Ia digunakan untuk mengalirkan gas dari silinder ke sumpitan api. Tahan api dan tahan pada tekanan tinggi. Hos boleh didapati dalam rekabentuk berkembar dan juga tunggal. Namun begitu hos berkembar mempunyai cirri-ciri keselamatan yang tinggi.
7.10 Prinsip Serta Jenis Sumpitan Api
Sumpitan api kimpalan adalah alat yang digunakan untuk mengeluarkan nyalaan hasil percampuran antara gas oksigen dan asetilina didalam ruang percampuran di dalam badan sumpitan api berkenaan. Nyalaan oksi-asetilina itu dikawal oleh dua injap yang terdapat dibadan sumpitan api. Injap-injap itu ialah injap oksigen dan injap asetilina.
Saiz muncung sumpitan api boleh didapati dalam berbagai saiz dan juga rekabentuk yang berlainan. Nombor bagi saiz muncung sumpitan dicetak pada panglal muncung. Muncung sumpitan juga boleh di dapati dalam berbagai rekabentuk dan jenama.
Alat-alat penyambung adalah terdiri daripada nat-nat berbenang dalam dan juga ‘nipple’ bagi menghubungkan hos dengan alatur dan juga badan sumpitan api. Kebanyakan alat penyambung ini diperbuat daripada gangsa dan aluminium.
Contoh 7.4
Mengapakah arah bebenang oksigen dibuat berbeza dengan bebenag asetilin?
Penyelesaian:
Bebenang oksigen dan bebnang asetilina mempunyai arah yang berlainan kerana semata-mata untuk tidak tersalah demi keselamatan alat dan jurukimpal.
7.11 Badan sumpitan-api
Badan sumpitan api adalah sebahagian daripada kelengkapan dalam pemasangan oksi-asetilina. Ianya berfunsi sebagai alat untuk mencampurkan gas asetilina dan oksigen mengikut nisbah yang tertentu bagi menghasilkan jenis nyalaan yang diperlukan.
7.11.1 Jenis-jenis badan sumpitan-api.
Terdapat dua jenis badan sumpitan-api yang digunakan, Iaitu:
i.Jenis tekanan seimbang
ii. Jenis injector
Badan sumpitan api tekanan seimbang ialah dimana kedua-dua gas akan masuk dan bercampur di dalam ruang percampuran. Manakala Badan sumpitan-api tekanan tinggi dimana pengaliran oksigen pada kelajuan yang lebih tinggi akan bercampur dengan gas asetilina sebelum memasuki ruang percampuran dan ianya digunakan jika janakuasa tekanan rendah digunakan
7.12 Sistem Pancarongga Kimpalan Gas.
Sistem pancarongga adalah satu anifo pemasangan kimpalan gas dimana silinder-silinder gas oksigen dan asetilina dikumpulkan disatu tempat berasingan diantara keduanya. Penyaluran gas bagi kedua-duanya akan disalurkan melalui paip keluli ke setiap setesen kimpalan.
Bagi anifo tunggal pula silinder oksigen dan asetilina akan digandingkan bersama-sama disetiap setesen kimpalan. Tetapi cara ini mempunyai anif-ciri keselamatan yang rendah dan tidak begitu menjimatkan penggunaan gas.
Oleh itu anifo pancarongga mempunyai anif-ciri keselamatan yang tinggi serta penjimatan dalam penggunaan gas berbanding anifo tunggal. Lebih-lebih lagi apabila banyak setesen beroperasi serentak. Ruang kerja pada setiap stesen kimpalan juga akan jadi lebih luas dan selesa.
Contoh 7.5
Apakah kebaikan menggunakan system anifold dalam pemasangan kimpalan oksi-asetilina?
Penyelesaian:
Sisitem Manifol adalah system yang paling selamat dan menjimatkan gas digunakan untuk kerja kimpalan gas kerana:
- silinder-selinder oksigen dan asetilina diletakan pada tempat yang berlainan.
- System ini mempunyai sebuah alator pusat yang mengawal tekanan ke tempat kerja.
- Menjimatkan ruang tempat bekerja
- Menggunakan gas secara maksima
LOJI KUASA STIM
Pengenalan
Sebuah loji kuasa stim menggunakan tenaga haba yang dihasilkan dari pembakaran bahan api seperti minyak diesel, arang batu atau bahan-bahan lain yang boleh dibakar untuk menghasilkan tenaga elektrik. Loji jenis ini digunakan secara meluas di muka bumi.
Loji ini menggunakan kitar Rankine. Kitar ini menerangkan stim yang dihasilkan oleh dandang, kemudian dihantar ke turbin stim ( penggerak utama ). Dari turbin, stim disejukkan kembali menjadi air yang berlaku di pemelowap, menghasilkan air tersebut disuap balik ke dandang untuk mengulangi proses penghasilan stim semula.
Kerana kepelbagaian bahan api yang boleh digunakan, loji jenis ini boleh digunakan untuk menghasilkan jumlah tenaga elektrik yang lebih besar. Di kebanyakan negara, loji ini dijadikan loji muatan pengkalan. Ini kerana loji kuasa stim lambat untuk dihidupkan dan tidak boleh digunakan sebagai pembekal tenaga untuk muatan kemuncak yang umumnya berlaku pada waktu yang singkat.
Loji kuasa ini yang digunakan bersama loji kuasa nuklear dijalankan hampir kepada keupayaan sepenuhnya untuk tempoh 24 jam sehari. Loji ini mempunyai tempoh hayat dari 30-40 tahun.
Gambarajah asas operasi loji kuasa stim
LOJI TURBIN GAS
Pengenalan
Sebuah loji kuasa turbin gas menggunakan turbin gas sebagai penggerak utama untuk menghasilkan tenaga elektrik.
Loji kuasa ini secara umumnya digunakan bersama loji kuasa stim. Loji kuasa jenis ini boleh digunakan untuk menghasilkan jumlah tenaga elektrik yang terhad. Di kebanyakan negara loji kuasa ini digunakan sebagai loji kuasa kemuncak.
Operasi
Loji kuasa ini di jalankan dengan menggunakan gas asli sebagai bahan api. Turbin menyedut angin di bahagian hadapannya, kemudian memampat, bercampur dengan bahan api dan menyalakan campuran udara mampat dan gas asli pada tekanan tinggi. Gas panas yang dilepaskan mengembang melalui bilah turbin, yang dihubungkan dengan syaf turbin. Syaf bergerak seterusnya menghasilkan tenaga mekanikal yang kemudiannya ditukarkan menjadi tenaga elektrik oleh penjana.
Gambarajah asas loji turbin gas.
LOJI KUASA NUKLEAR
Pengenalan
Sebuah loji kuasa nuklear menggunakan tenaga nuklear untuk menjana tenaga elektrik.
Loji kuasa ini secara umumnya terletak jauh dari kawasan yang berpopulasi. Loji kuasa jenis ini boleh digunakan untuk menghasilkan tenaga elektrik dengan jumlah lebih besar. Di kebanyakan negara loji ini dijadikan sebagai loji kuasa muatan pengkalan. Ini kerana ia boleh mengambil masa selama beberapa hari untuk dipanaskan dan digunakan untuk operasi.
Operasi
Elemen-elemen yang berat seperti Uranium (U235) atau Thorium (Th232) adalah subjek kepada pembelahan tenaga nuklear dalam sebuah reaktor untuk menghasilkan stim bersuhu dan bertekanan tinggi.
Stim menggerakkan turbin stim yang menukarkan tenaga nuklear ini kepada tenaga mekanikal.
Turbin stim kemudiannya menjalankan pengulang-alik yang menukarkan tenaga mekanikal kepada tenaga elektrik.
Gambarajah asas operasi loji kuasa nuklear
Automotive Air Conditioning System
Introduction about automotive air conditioning :
Hardware Tool
1) Evaporator
2) Motor
3) Speed Meter
4) Power Supply
5) Compresser
6) Condenser
7) Control Panel Box
8) Refrigerant flow meter
9) Thermo meter
10) Variable AC motor Drives
Today, as we drive our automobiles, a great many of us, can enjoy the same comfort levels that we are accustomed to at home and at work. With the push of a button or the slide of a lever, we make the seamless transition from heating to cooling and back again without ever wondering how this change occurs. That is, unless something goes awry.
Since the advent of the automotive air conditioning system in the 1940's, many things have undergone extensive change. Improvements, such as computerized automatic temperature control (which allow you to set the desired temperature and have the system adjust automatically) and improvements to overall durability, have added complexity to today's modern air conditioning system. Unfortunately, the days of "do-it-yourself" repair to these systems, is almost a thing of the past.
To add to the complications, we now have tough environmental regulations that govern the very simplest of tasks, such as recharging the system with refrigerant R12 commonly referred to as Freon® (Freon is the trade name for the refrigerant R-12, that was manufactured by DuPont). Extensive scientific studies have proven the damaging effects of this refrigerant to our ozone layer, and its manufacture has been banned by the U.S. and many other countries that have joined together to sign the Montreal Protocol, a landmark agreement that was introduced in the 1980's to limit the production and use of chemicals known to deplete the ozone layer.
Now more than ever, your auto mechanic is at the mercy of this new environmental legislation. Not only is he required to be certified to purchase refrigerant and repair your air conditioner, his shop must also incur the cost of purchasing expensive dedicated equipment that insures the capture of these ozone depleting chemicals, should the system be opened up for repair. Simply put, if your mechanic has to spend more to repair your vehicle - he will have to charge you more. Basic knowledge of your air conditioning system is important, as this will allow you to make a more informed decision on your repair options.
Should a major problem arise from your air conditioner, you may encounter new terminology. Words like "retrofit" and "alternative refrigerant" are now in your mechanics glossary. You may be given an option of "retrofitting", as opposed to merely repairing and recharging with Freon. Retrofitting involves making the necessary changes to your system, which will allow it to use the new industry accepted, "environmentally friendly" refrigerant, R-134a. This new refrigerant has a higher operating pressure, therefore, your system, dependant on age, may require larger or more robust parts to counter its inherent high pressure characteristics. This, in some cases, will add significantly to the final cost of the repair. And if not performed properly, may reduce cooling efficiency which equates to higher operating costs and reduced comfort.

COMPRESSOR, CONDENSER, EVAPORATOR, ORIFICE TUBE, THERMAL EXPANSION VALVE , RECEIVER-DRIER,ACCUMULATOR. Note: if your car has an Orifice tube, it will not have a Thermal Expansion Valve as these two devices serve the same purpose. Also, you will either have a Receiver-Dryer or an Accumulator, but not both.
JURUTERA MEKANIKAL ISLAM-IBNU ISMAIL AL JAZARI
KINCIR air atau noria di Fayyoum, Mesir, adalah sebahagian kecil pembaharuan yang berlaku pada zaman kegemilangan empayar Islam yang menjana pertumbuhan penduduk di kawasan pedalaman daripada tradisi nomad kepada penempatan tetap.
Di bawah empayar Islam, perkembangan sistem saliran diperbaiki sehingga tidak lagi bergantung kepada tenaga manusia atau haiwan.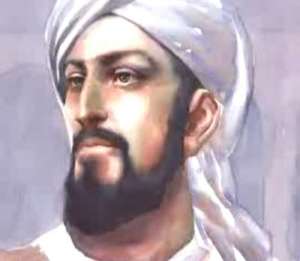
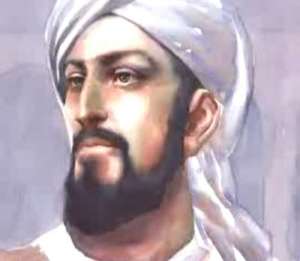
Mekanisme kejuruteraan inilah melahirkan istilah baru, ‘automata’ atau automatik yang bermakna berjalan dengan sendiri oleh tabii alam.
Menerusi mekanisma itu, penggunaan air dibentuk dalam dwifungsi, arus air menjadi penolak alat takungan ke kedudukan atas berulang kali dengan bantuan graviti, sambil saliran air disalurkan untuk keperluan diri dan tanaman.
Ilmu pengetahuan dan ciptaan kincir air yang kemudiannya memberi inspirasi kepada bidang kejuruteraan moden ini adalah hasil kepakaran tokoh terkenal, Al-Jazari atau nama sebenarnya Badi Al-Zaman Abullezz Ibn Alrazz Al-Jazari.
Beliau digelar Al-Jazari mengambil sempena nama tempat kelahirannya di Al-Jazira, sebuah wilayah yang terletak di antara Tigris dan Efrat, Iraq.
Kegemilangan Al-Jazari adalah hasil manuskrip beliau berjudul ‘Kitab fi ma’rifat al-hiyal al-handasiyya’ yang bermaksud ‘buku mengenai ilmu alat mekanikal yang bijak’.
Manuskrip itu menjadi bukti catatan terawal penggunaan engkol, piston dan injap yang digunakan untuk menghasilkan produk yang menjadi kegunaan harian masyarakat pada waktu itu seperti mesin pengepam air.
Sememangnya masyarakat dulu memang sudah lama memanfaatkan peralatan untuk mendapatkan air menggunakan shaduf, alat yang terdiri daripada blok panjang diletakkan antara dua tiang dengan blok kayu mendatar.
Peralatan lain ialah saqiya, di mana mekanisma tengahnya terdiri dari dua gigi dan mesin itu menggunakan tenaga haiwan seperti unta atau keldai.
Ilmuwan Muslim melakukan penyelidikan mengenai peralatan berkenaan untuk mendapatkan hasil lebih memuaskan termasuk Al-Jazari yang merintis jalan menghasilkan mesin mengepam air.
Dua mesin pertama ciptaannya adalah hasil pengubahsuaian shaduf dan yang ketiga saqiya di mana tenaga air digunakan menggantikan tenaga binatang.
Mesin yang sama seperti saqiya di letakkan di sungai Yazid di Damsyik bagi kegunaan rumah sakit yang terletak berdekatan sungai itu.
Hasil ciptaannya kelima ialah mesin yang menggunakan engkol, alat yang menghasilkan gerakan berterusan dan penemuan itu berjaya mencipta sejarah kerana engkol adalah peralatan mekanik paling penting bagi orang Eropah awal abad ke-15.
Al-Jazari mengembangkan mesin engkol yang dihubungkan dengan sistem rod pada mesin pengepam air dan ini dilakukan beliau pada 1206.
Beliau juga menghasilkan mesin yang digerakkan oleh air bagi menggerakkan piston yang saling berhubungan dengan paip penyedut pada dan ia adalah contoh prinsip double acting yang pertama.
Al Jazari kemudian mengumpulkan semua hasil karyanya berkaitan bidang teknikal yang lengkap dengan maklumat dari segi teori dan praktikal dalam buku berjudul Al-Jami Baim Al-Ilm wal Amal Al-Nafi Fi Sinat’at Al Hiyal.
Berkat kemampuan mekaniknya, al-Jazari tercatat mampu merakit beberapa jenis jam air. “Salah satunya, sebuah jam dengan tenaga air yang tingginya satu meter dan lebarnya satu setengah meter. Jam itu berhasil direkonstruksi di Museum Ilmu Pengetahuan tahun 1976,” ungkap Donald Routledge Hill dalam karyanya A History of Engineering in Classical and Medieval Times.
Al-Jazari juga mampu membuat jam air berbentuk gajah. Bahkan, jam buatan al-Jazari sudah mampu menghasilkan suara. Dalam manuskrip al-Jazari, jam itu merupakan jam terawal yang menggunakan flow regulator, sebuah sistem tutup-lubang dan sebuah otomaton seperti sebuah jam burung.
“Jam ini merupakan jam pertama dengan reaksi otomatis dalam interval waktu. Jam ini menggunakan sebuah robot manusia (humanoid) yang membentur gembreng dan sebuah robot burung mekanik secara otomatis bersiul. Jam air ini juga dikenal sebagai jam pertama yang bisa merekam waktu secara akurat untuk menyesuaikan lamanya hari yang tidak sama sepanjang tahun,” imbuh al-Hassan dan Hill.
Rancangan jam air buatan al-Jazari juga diakui sangat bagus. ”Jam al-Jazari penuh dengan ide-ide dan teknik-teknik yang penting bagi sejarah perancangan mesin,” kata al-Hassan dan Hill.
Karyanya berbeza dengan karya ilmuwan lain kerana beliau memberi penerangan terperinci mengenai ilmu mekanikal yang mengandungi 50 peralatan yang dibahagikan kepada enam kategori.
Antaranya, jam air, alat mencuci tangan dan mesin pengepam air. Jam air adalah hasil kerja gemilang Al-Jazari yang dikagumi pada acara World of Islam Festival pada 1976.
Karya beliau juga dianggap sebagai sebuah manuskrip terkenal di dunia dan menjadi teks penting untuk mempelajari sejarah teknologi kerana dilengkapi ilustrasi menakjubkan.
Dengan karya gemilangnya, ilmuwan dan jurutera Islam yang mengabadikan diri di istana Artuqid di bawah naungan Sultan Nasir al-Din Mahmoud telah membawa masyarakat Islam pada abad ke-12 kepada kejayaan.
Jurutera Inggeris, Donald Hill yang tertarik dengan karya Al-Jazari menterjemahkan bukunya pada 1974.
Pendekatan Al-Jazari yang menjadi asas kepada perkembangan teknologi industri pada abad ke-18, diakui pakar tempatan, pensyarah dan juga penyelidik Fakulti Kejuruteraan Universiti Kebangsaan Malaysia (UKM), Prof Dr Wan Ramli Wan Daud.
Beliau bersama kumpulannya berjaya mencipta enjin menggunakan tenaga sel kimia berkuasa 200 watt bagi menggerakkan motosikal.
Menurut Wan Ramli, apa yang diperlukan sekarang ialah menyuntik semula semangat yang dijelmakan oleh ilmuwan seperti Al-Jazari, dengan menghasilkan ciptaan untuk kesejahteraan sejagat.
OBJEKTIF AM
Dapat mengetahui jenis-jenis mesin larik dan mata alat serta berkebolehan mengendalikan mesin larik.
OBJEKTIF KHUSUS
Di akhir unit ini anda sepatutnya dapat :
Mengenali jenis-jenis mesin larik.
Mengetahui fungsi bahagian-bahagian mesin larik tetengah.
Mengetahui kaedah bagaimana benda kerja dipegang pada mesin larik.
Memahami fungsi dan jenis-jenis mata alat.
Mengetahui sudut-sudut yang ada pada mata alat.
Mengetahui jenis bahan dan kegunaan mata alat.
Mengetahui langkah pengendalian kerja-kerja menggerek, menggerudi, melorek, melarik tirus, memotong ulir skru dan melarik tak sepusat.
6.0 PENGENALAN
Mesin larik ialah satu-satunya mesin yang paling versatil dalam bengkel kejuruteraan. Walaupun pelbagai betuk mesin pelarik telah digunakan sebelum kurun ke-18, nanun mesin pelarik pertama yang boleh memotong ulir hanya dicipta pada tahun 1797 oleh seorang mekanik Inggeris bernama Henry Maudslay. Mesin ciptaan beliau telah banyak digunakan dalam pembinaan enjin stim kereta api rekaan James Watt pada awal kurun ke-19 iaitu pada zaman revolusi industri England.sejak dari masa itu mesin ini telah diperbaiki dan ditambah dengan beberapa alatan tambahan supaya dapat mengeluarkan komponen-komponen dengan tepat dan persis. Di Malaysia mesin ini amat popular sehingga setiap bengkel kejuruteraan mempunyai sekurang-kurangnya sebuah mesin.
JENIS-JENIS MESIN LARIK
Mesin pelarik boleh dijumpai dalam beberapa bentuk dan saiz. Jenis yang terkecil digunakan dalam pengeluaran komponen kecil jam tangan sementara yang besar sekali digunakan untuk memesin syaf berat. Mesin pelarik boleh dikelaskan kepada dua kategori :
Mesin Pelarik Jentera
Dalam kategori ini terdapat empat jenis mesin pelarik.
1) Jenis bangku
Mesin ini kecil dan boleh dipasang diatas bangku atau kabinet besi. Ia digunakan untuk menghasilkan kerja yang ringan dan halus.
2) Mesin pelarik piawai (mesin larik tetengah)
Mesin ini lebih besar dan berat daripada jenis bangku. Panjang landasan mesin adalah 1.5 meter hingga 6 meter. Lazimnya mesin ini digunakan untuk kerja-kerja penyelenggaraan sederhana dan juga dalam institusi latihan kemahiran.
3) Jenis toolroom
Jenis mesin ini lebih persis dan digunakan dalam pembinaan Tool dan Die. Mesin ini juga dilengkapi dengan alat tambahan khas dan aksesori supaya beberapa operasi Tool dan Die boleh dilakukan.
4) Jenis gap-bed
Saiz mesin ini lebih besar daripada jenis bangku. Sebahagian daripada landasannya di bawah cuk boleh ditanggalkan supaya bahan kerja atau kompenen dengan diameter yang lebih besar boleh dipegang.
Jenis Mesin Pengeluaran
Ada lima jenis mesin pelarik untuk kategori ini :
(a) Pelarik turret pelana
Pelarik turret pelana juga disebut jenis mesin pelarik turret. Mesin ini mempunyai kepala turret yang dipasang pada pelana yang bergerak diatas landasan. Kepala turret boleh memegang beberapa jenis mata pemotong dan boleh digunakan untuk melarik beberapa operasi tanpa memberhentikan mesin untuk menukar mata alat.
(b) Pelarik kapstan
Pelarik kapstan juga disebut pelarik turret pelantak. Mesin ini kecil sedikit saiznya daripada jenis pelarik turret. Ia digunakan untuk melakukan kerja-kerja sederhana dan ringan sahaja. Kepala turret mesin ini terletak diatas satu kekesot berbentuk landasan pendek. Landasan pendek ini pula menggelongsor diatas landasan utama mesin dan boleh dikunci pada sebarang kedudukan yang dikehendaki.
(c) Pelarik automatik
Jenis mesin pelarik automatik dicipta untuk pengeluaran kuantiti diantara beberapa ratus sehingga beberapa puluh ribu kompenen sehari. Semua pergerakan mata pemotong dan bahan kerja dikawal oleh sesondol (cam), sistem hidraulik atau sistem elektro mekanik.
d) Pelarik kegunaan khas
Pelarik jenis ini dicipta untuk melakukan kerja-kerja khas seperti :
*pelarik roda kereta api
*pelarik aksel
*pelarik penampang
*pelarik menegak
(e) Pelarik N.C dan C.N.C
Mesin pelarik terbaru ini berfungsi dibawah kawalan komputer. Mesin ini lebih produktif dan hasil pengeluarannya lebih persis jika dibandingkan dengan mesin lain. Terdapat dua jenis mesin iaitu :
*Jenis yang mempunyai turret dipasang pada landasan mesin sahaja.
*Jenis yang mempunkyai dua turret dimana satu turret dipasang pada landasan dan satu lagi pada kekesot lintang.
FUNGSI BAHAGIAN-BAHAGIAN MESIN LARIK TETENGAH
Bahagian-bahagian utama mesin pelarik terdiri daripada landasan, alatan hadapan, alatan belakang, kekotak gear cepat tukar dan kereta.
1) Landasan
(a) Landasan adalah tulang belakang sebuah mesin pelarik. Kejituan mesin pelarik bergantung pada ketegaran, penjajaran dan ketepatan pada landasannya.
(b) Bahagian atas landasan boleh berbentuk ‘V’ atau rata dan diatasnya terletak peralatan lain seperti alatan hadapan, kereta dan alatan hadapan.
(c) Landasan diperbuat daripada besi tuangan yang bermutu tinggi. Rawatan haba kekerasan dilakukan keatasnya supaya boleh tahan haus.
2) Alatan hadapan
(a) Bahagian ini terletak di sebelah kiri landasan mesin.
(b) Spindal utama yang berbentuk satu syaf geronggang yang disokong oleh beberapa galas terletak di dalam bahagian ini. Hujunjg spindal atau muncungnya yang terkeluar daripada alatan hadapan yang berbentuk jenis tirus, jenis ulir atau jenis kekunci sesondol ( kam lock )
(c) Pada hujung spindal ini beberapa peraltan seperti cuk, piring pelarik dan tetengah hidup boleh dipasang dan digunakan untk memegang bahan kerja atau kompenen yang hendak dilarik.
(d) Untuk memutarkan spindal utama, alatan hadapan mempunyai perlatan takal atau beberapa siri rangkaian gear. Alatan hadapan bergear mempunyai lebih rangkaian kelajuan dan lebih tepat putarannya jika dibandingkan dengan alatan hadapan yang bertakal. Lagipun takal boleh tergelincir bila terkena minyak dan ini menyebabkan hasil larikan yang tidak rata atau licin.
3 Alatan Belakang
(a) Bahagian ini terletak disebelah kanan landasan. Ia boleh digerakan disepanjang landasan dan juga boleh dikunci pada mana-mana kedudukan yang dikehendaki. Alatan belakang terdiri daripada dua bahagian utama, badan dan tapak.
(b) Pada badan terdapat satu spindal yang mempunyai penirusan piawaian Morse. Alat pemotong bertangkai tirus Morse, seperti gerudi dan pelulas boleh dipasang pada spindal tersebut.
(c) Tapak alatan belakang dimesin dengan jitu supaya boleh didudukan diatas landasan dengan tepat. Pada tapak terdapat dua skru penyelaras yang diguna untuk menjajarkan keselarian diantara tetengah mati dan tetengah hidup atau mengofsetkan alatan belakang supaya dapat melarik tuirus dengan kaedh ini.
4) Kotak gear cepat tukar
(a) Kotak gear terletak disebelah kiri landasan dan dibawah alatan hadapan. Kotak ini mempunyai beberapa gear berbilang saiz untuk memutarkan skru pemandu atau aci penghantar.
b) Skru pemandu digunakan untuk memajukan kereta semasa memotong ulir. Aci penghantar pula digunakan semasa membuat kadar penghantaran yang tertentu secara otomatik.
5) Kereta
(a) Sela
Bahagian ini ialah tuangan berbentuk huruf H dan boleh bergerak diatas landasan. Apron dan kekesot lintang dipasang pada sela.
(b)
Apron
Bahagian apron dipasang dihadapan sela dengan bolt. Apron mempunyai beberapa gear dan peralatan yang digunakan untuk mengawal pergerakan sela dan kekesot lintang. Satu tuas tangan yang dipasang dengan pinan jejaring dengan rak terletak dibawah landasan. Tuas tangan ini diputarkan apabila hendak menggerakkan kereta secara insani ( manual ). Keseluruhan bahagian kereta dan kekesott lintan boleh digerakkan secara otomatik atau insani
(c) Kekesot Lintang
Tiang mata alat dipasang pada kekesot bergabung. Kekesot bergabung pula dipasang diatas kekesot lintang dengan dua bolt. Apabila kedua-dua bolt ini dilonggarkan kekesot bergbung boleh dikilaskan pada sudut yang dikehendaki. Dengan cara ini penirusan tajam tetapi pendek boleh dilarik. Pada hujung kekesot lintang dan kekesot bergabung dilengkapi dengan relang yang ditanda jitu supaya kedalaman pemotongan dapat dilaraskan dengan tepat.
KAEDAH MEMEGANG BAHAN KERJA DI MESIN LARIK
Kaedah memegang bahan kerja dengan bindu
Jenis-jenis muncung spindal
Terdapat tiga jenis muncung spindal yang biasa terdapat pada mesin pelarik. Aksesori seperti pelbagai jenis cuk dan piring pelarik dipasang pada muncung ini. Tiga jenis muncung spindal adalah :
(1) Jenis berulir
Muncung spindal jenis berulir biasanya terdapat pada mesin-mesin kecil dan yang lama. Ulir yang terdapat pada muncung ini biasanya dari jenis bentuk ‘V’. Satu plat penyesuai yang mempunyai ulir dalam dan bentuk yang sama, dipasang pada belakang cuk. Semasa memmasang cuk ini pada muncung spindal dua perkara yang perlu diperhatikan ialah :
(a) Ulir luar dan dalam mestilah bersih. Kalau tidak pemasangan akan menjadi tidak tepat.
(b) Ulir luar pada muncung spindal tidak rosak atau sumbing, kerana ini akan menyebabkan cuk tidak boleh dipasang.
(2) Jenis tirus Amerika
Muncung spindal ini bertirus piawai Amerika iaitu 89 mm untuk setiap 305 mm (3.5 inci untuk setiap kaki). Tirus ini tajam dan membolehkan aksesori seperti cuk dan pirin pelarik dibersih dan dipasang atau ditanggal dengan pantas. Satu kekunci pada muncung tirusdigunakan untuk menempatkan cuk atau piring pelarik pada kedudukan yang tepat. Gelang kekunci yang berulir itu pula digunakan untuk mengikat cuk pada spindal utama mesin.
(3) jenis Kam-Lock
Permukaan muncung spindal ini mempunyai tiga atau enam lubang telusan. Fungsi lubang ini adalah untuk menempatkan dan mengunci stad kekunci sesondol yang ada pada aksesori yang perlu dipasang. Separa putaran kam-lock akan melepaskan stad ini dan membolehkan aksesori itu dikeluarkan dengan mudah dan cepat. Dari segi penggunaan, jenis kam-lock adalah cepat jika dibandingkan dengan yang lain.
Rajah dibawah menunjukkan tiga kaedah digunakan untuk memegang bahan kerja dengan cuk tiga rahang. Walaubagaimanapun berhati-hatilah semasa menggunakan kaedah seperti ditunjukkan dalam rajah (a) dan (c) kerana kaedah ini bahan kerja munngkin tergelincir keluar jika hantaran dan kedalaman pemotongan berlebihan dilakukan. Bahan kerja bulat dan berbentuk heksagon boleh dipegang dengan cuk tiga rahang.
Kaedah memegang bahan kerja dengan cuk empat rahang
Rajah dibawah menunjukan tiga kaedah yang digunakan untuk memegang bahan kerja dengan cuk empat rahang. Bahan kerja boleh dipegang dengan lebih persis dengan cuk jenis ini dari cuk tiga rahang. Pemusatan bahan kerja secara kasar boleh dilakukan dengan bantuan lengkung sepusat yang ada pada muka cuk. Dua cara yang lebih persis adalah dengan bantuan tolok permukaan dan tolok dail.
Kaedah memegang bahan kerja dengan cuk kolet
Rajah dibawah menunjukkan kaedah memegang bahn kerja dengan cuk kolet jenis ‘draw back’. Cuk kolet ini biasanya digunakan untuk memegang dan memesin komponen-komponen yang kecil dengan cepat dan tepat. Untuk mengunci, bar penarik diputarkan dan ini menyebabkan kolet ditarik ke dalam sarung tirus. Proses ini membolehkan kolet mencengkam bahan kerja dengan lebih jitu dan tepat.
Kedah memegang dengan sangga tetap
Rajah dibawah menunjukkan kaedah memegang bahan kerja dengan sangga tetap. Aksesori ini palingsesuai sekali digunakan untuk menyokong bahan kerja yang panjang dan yang perlu dimesin pada hujungnya. Biasanya bahan kerja yang ukuran panjangnya 3 kali ganda diameter perlu disokong oleh sangga atau tetengah untuk mengelak bahan kerja dari bengkok atau memegas (spring).
Kaedah memegang dengan sangga bergerak
Rajah dibawah menunjukkan kaedah penggunaan sangga bergerak semasa melarik bahan kerja yang panjang. Sanggabergerak mengelakkan bahan kerja memegas pada kedudukan mata alat semasa proses memesin sedang dijalankan. Amat sesuai digunakan semasa melarik selari pada bahan kerja yang berdiameter kecil dan panjang.
Lelabah
Rajah dibawah menunjukkan sebuah lelabah (spider) dan penggunaannya. Lelabah biasanya digunakan untuk menyokong paip atau tiub yang panjang. Satu hujung dipegang pada cuk tiga rahang dan satu lagi dipasang dengan lelabah. Pada pusat lelabah terdapat lubang tetengah dimana tetengah dipasangkan.
Kepala kekucing
Rajah dibawah menunjukkan kepala kekucing. Alat ini perlu digunakan bersama
dengan sangga tetap. Kepala kekucing berfungsi sebagai penyokong dan
pengalas untuk syaf yang panjang. Syaf ini mungkin telah dimesin dengan jitu
dan licin. Dengan penggunaan kepala kekucing permukaan syaf boleh dielak dari
tercalar semasa melarik. Syaf panjang yang berbentuk heksagon juga boleh
dipasang dengan kepala kekucing supaya dapat disangga dengan mudah.
MEMAHAMI FUNGSI DAN JENIS-JENIS MATA ALAT
Faktor yang menentukan kecekapan sebuah mesin larik ialah bentuk dan jenis mata alat yang digunakan. Bahan mata alat yang digunakan haruslah memepunyai sifat-sifat berikut:
(a) Bahan mestilah keras
(b) Mempunyai rintangan kehausan
(c) Menahan sifat kekerasan pada suhu yang tinggi semasa memotong
(d) Menyerap kejutan semasa melakukan operasi seperti melarik eksentrik dan larikan kasar.
Diantara jenis-jenis mata alat yang biasa digunakan bagi kerja-kerja melarik biasa ialah :
a. Mata alat pemotongan biasa
b. Mata alat melurah
c. Mata alat membenang
-Jenis ‘V’
-Jenis Acme
-Jenis Buttres
-Jenis Bersegi
d. Mata alat jenis sisip (Throwaway)
e. Mata alat menggerek dan sebagainya
SUDUT-SUDUT YANG ADA PADA MATA ALAT
SUDUT SADAK ATAS (top rake)
Fungsi utama sudut ini adalah dalam pengeluaran tatal semasa larikan dibuat. (sudut ini curam positif atau negetif, lihat rajah). Sudut ini bergantung kepada jenis bahan yang dipotong. Sudut sadak atas untuk bahan lembut seperti loyang adalah lebih besar daripada misalnya bahan keluli lembut. Untuk memesin yang terlalu keras atau lembut sudut sadak atas dicadangkan bersudut negetif.
SUDUT SADAK TEPI
Sudut ini bergantung kepada bahan yang dilarik dan jenis operasi yang dilakukan, contohnya melarik kasar, penyudahan dan sebagainya. Sudut tepi yang besar membolehkan tatal keluar dengan mudah dan mengurangkan geseran tetapi melemahkan sudut pemotongan. Sudut sadak tepi yang kecil dan negetif akan memperkuatkan sudut pemotongan tetapi ini akan menjejaskan pengeluaran tatal dan akan menambahkan bebanan keatas mata alat.
SUDUT TELUSAN HADAPAN
Sudut telusan hadapan mengelakan mata alat daripada menggesel bahan kerja yang dimesin. Saiz sudut ini bergantung pada kadar dataran dan diameter bahan kerja yang dimesin. Jika sudut ini terlalu kecil, mata alat akan menggesel bahan kerja dan tidak akan memotong dengan baik serta menghasilkan penyudahan yang kasar. Jika terlalu besar pula, poin mata alat akan menjadi lemah, mudah terbakar dan patah.
SUDUT TELUSAN TEPI
Sudut telusan tepi bergantung kepada kekerasan bahan yang dilarik dan kadar hantaran pemotongan. Untuk bahan kerja keluli sudutnya adalah antara 6 hingga 10 dan untuk bahan yang lebih keras suditnya adalah 4. sudut ini boleh dikurangkan jika berlaku gelatuk (chatter). Sebaliknya sudut ini ditambah jika berlaku getaran.
SUDUT PEMOTONG TEPI
Sudut ini adalah antara 10 hingga 25 dan bergantung kepada aplikasinya, mislnya operasi jenis melarik penampang, melarik kasar dan sebagainya. Jika sudut pemotong tepi terlalu besar ini akan menyebabkan mata alat menggelatuk.
SUDUT PEMOTONG HUJUNG
Sudut ini juga boleh berubah mengikut aplikasinya. Untuk melarik kasar suduut 5 hingga 15 digunakan. Sudut yang kecil akan memperkukuhkan hujung mata alat. Untuk melarik biasa sudutnya antara 15 hingga 30. Sudut yang besar mata alat dikilas kekiri supaya operasi melarik bahu dan larikan hampir dengan cuk boleh dilakukan.
OBJEKTIF AM
Memahami konsep kimpalan gas serta serta kegunaannya dalam bidang perindustrian.
OBJEKTIF KHUSUS
Mendefinasikan kimpalan gas dan menerangkan perkara-perkara yang berkaitan dengannya iaitu:
Kimpalan gas tekanan tinggi dan
kimpalan gas tekanan rendah.
Kegunaan kimpalan gas dalam
industri.
Jenis-jenis gas untuk kegunaan kimpalan
gas.
Sifat gas oksigen, cara pengeluaran dan
silinder oksigen.
Sifat-sifat gas asetilina ,cara pengeluaran
dan silinder asetlina.
Jenis-jenis gas sebagai bahan bakar.
Kelengkapan kimpalan gas oksi-asetilina.
Tugas serta prinsip-prinsip alatur satu
peringkat dan dua peringkat.
Jenis-jenis hos untuk kimplan oksi-
asetilina.
Prinsip serta jenis-jenis sumpitan api.
Sistem pancarongga dan sistem stesen
tunggal kimpalan oksi-asetilina.
7.0 PENGENALAN:
‘Kimpalan Gas’ adalah satu cabang daripada kerja kimpalan yang telah lama diamalkan dalam bidang industri. Terutama sekali dalam bidang fabrikasi logam. Ini adalah kerana kimpalan gas adalah didapati amat sesuai untuk kepingan logam-logam yang nipis. Contoh bidang kerja yang melibatkan proses kimpalan gas ialah kerja membaikpulih badan kenderaan serta kerja-kerja fabrikasi logam yang melibatkan kepingan logam nipis.
Pada awal kurun kedua-puluh manusia telah mengetahui cara menyambung logam dengan memanaskan dua batang logam hingga merah menyala dan seterusnya impak yang kuat dikenakan ke atas kedua-duanya sehinggalah kedua-duanya bercantum menjadi satu. Proses ini dipanggil sebagai kimpalan tempa. Kaedah ini telah diperbaiki dari masa kesemasa seiring dengan perkembangan teknologi sehinggalah kaedah terkini kimpalan gas telah dapat kita semua gunakan sekarang ini.
7.1 Definasi Kimpalan Gas
Kimpalan gas didefinasikan sebagai satu proses penyambungan logam dengan kaedah memanaskan kedua-dua bahagian logam yang hendak disambung sehingga cair dan bercantum menjadi satu.
7.2 Kimpalan Gas Tekanan Rendah Dan Kimpalan Gas Tekanan Tinggi
7.2.1 Terdapat dua jenis kimpalan gas iaitu:
Kimpalan gas tekanan rendah
Kimpalan gas tekanan tinggi.
Kimpalan tekanan rendah menerima bekalan gas asetilina dari janakuasa gas asetilina yang mempunyai tekanan kurang dari 1.0 psi atau 1.0 Bar
Kimpalan gas tekanan tinggi menerima bekalan gas dari janakuasa gas asetilina yang mempunyai tekanan dari 1-15psi atau 1-15 Bar.
7.3 Kegunaan kimpalan gas dalam industri
Dalam bidang perindustrian kimpalan gas banyak digunakan dalam kerja fabrikasi logam yang melibatkan kepingan logam yang ketebalannya melebihi daripada 1.0mm sehingga 3.0mm. Contohnya, dalam kerja-kerja membaikpulih badan kenderaan yang melibatkan kerja-kerja ketuk mengetuk dan menampal bahagian-bahagian badan kenderaan yang rosak.
7.4 Gas
Dua jenis gas yang biasa digunakan dalam kerja kimpalan gas adalah oksigen(O ) dan asetilina (C H ). Campuran kedua-dua gas menghasilkan haba yang paling tinggi berbanding gas-gas bahanapi yang lainnya. Suhunya boleh mencapai sehingga 3316C.
7.5 Gas Oksigen
Gas oksigen tidak mempunyai warna , rasa dan bau. Ia juga merupakan sejenis gas yang dapat memebantu dalam proses pembakaran dan juga merupakan gas aktif yang boleh bertindakbalas ke atas logam yang menyebabkan pengoksidanan berlaku ke atas logam berkenaan. Contohnya, pengkaratan ke atas keluli.
7.5.1 Penghasilan Gas Oksigen
Gas oksigen boleh dihasil melalui beberapa kaedah, iaitu:
i) Kaedah penyulingan udara.(pemeringkatan udara)
ii) Kaedah elektrolisis
Kaedah penyulingan udara adalah satu kaedah yang dilakukan secara komersial. Ianya dilakukan melalui proses pengasingan oksigen daripada udara yang dipanggil proses penyulingan udara cair yang termampat pada ketekanan 206 bar (3000psi) iaitu pada suhu -160C. Seterus tekanan akan akan di kurangkan sedikit demi sedikit dimana oksigen dalam bentuk cair akan bertukar menjadi gas lalu ditabungkan. Begitulah bagi gas-gas yang lainnya akan bertukar menjadi gas apabila tekanan dikurangkan dan ditabungkan untuk kegunaan yang lain.
Kaedah elektrolisis adalah satu proses penghasilan gas oksigen yang diperolehi melalui arus elektrik di dalam air. Proses ini sangat mahal dan tidak ekonomi untuk dikomersialkan.
Gas oksigen akan disimpan dalam silinder keluli yang berwarna hitam dan
lebih tinggi daripada silinder asetilina. Ianya tidak bersambung dan berupaya menahan tekanan setinggi 3360 psi. Boleh didapati dalam tiga saiz.
Contoh 7.1
Apakah perbezaan antara kimpal an tekanan tinggi dan kimpalan tekanan rendah?
Penyelesaian:
- Kimpalan tekanan rendah menerima bekalan gas asetilina dari janakuasa gas asetilina yang mempunyai tekanan kurang dari 1.0 psi atau 1.0 Bar
- Kimpalan tekanan rendah menggunakan badan sumpitan
jenis ‘injector’
- Kimpalan gas tekanan tinggi menerima bekalan gas dari janakuasa gas asetilina yang mempunyai tekanan dari 1-15psi atau 1-15 Bar.
- Menggunakan badan sumpitan api jenis tekanan seimbang
7.6 Jenis-Jenis Gas Bahan Bakar
7.6.1 Gas Asetilina:
Gas asetilina adalah bahanapi yang tidak mempunyai warna tetapi mempunyai bau yang kuat dan mudah terbakar .Ia adalah gas yang tidak stabil dan perlu disimpan dalam keadaan yang tetap. Titik kritikal bagi gas asetilina ialah pada tekanan 28 psi pada suhu 70F.
Penghasilan gas asetilina:
Gas asetilina dapat dihasilkan dengan mencampurkan kalsium karbida dan air. Terdapat dua jenis janakuasa yang menghasikan gas asetilina, iaitu:
i) janakuasa tekanan rendah .
ii) janakuasa tekanan tinggi
Gas asetilina disimpan dalam silinder keluli berwarna maroon yang diisikan dengan bahan berliang sepenuhnya yang terdiri daripada habuk kayu balsa, arang kayu,simen,dan bahan-bahan telap yang lain.
Bahan-bahan telap yang dimuatkan ke dalam silinder asetilina adalah berfungsi untuk menyerap seberapa banyak cairan aseton. Aseton ini pula akan berfungsi untuk menyerap gas asetilana sebanyak 25 kali ganda isipadunya sendiri.
Contoh 7.2
Namakan dua jenis janakuasa dalam penghasilan gas asetilina.
Penyelesaian:
Dua jenis janakuasa gas asetilina ialah:
- Janakuasa tekanan tinggi (karbida kepada air – melebihi 20 meter padu )
- Janakuasa tekanan rendah.( air kepada karbida – kurang dari 20 meter padu )
7.6.2 Gas Bahanapi Yang Lain-Lain
Selain daripada asetilina terdapat juga gas-gas bahanapi yang lain yang mana campuran gas ini bersama oksigen akan menghasilkan suhu yang agak tinggi. Berikut adalah perbandingan suhu-suhu bagi campuran antara dua gas.
i) oksi-asetilina 3100C - 3500C
ii) udara-asetilina 2300C - 2500C
iii) oksi-hidrogen 2200C - 2382C
1v) oksi-gas arang batu 1982C - 2182C
7.7 Kelengkapan Kimpalan Gas
7.8 Tugas Serta Prinsip-Prinsip Alatur Satu Peringkat Dan Dua Peringkat
Adalah merupakan alat kawalan yang dipasang pada bahagian atas silinder oksigen atau asetilina bagi mengawal pengaliran gas yang diperlukan untuk tujuan mengimpal dan juga untuk menunjukkan tekanan gas dalam silinder. Ianya dikenali juga dengan tolok tekanan. Terdapat dua jenis alatur iaitu alator alatur satu peringkat dan dua peringkat.
Alator juga mempunyai rekabentuk dan jenama yang berbagai. Terdapat juga alator yang mempunyai satu tolok bacaan tetapi itu tidak menunjukkan bahawa ianya jenis satu peringkat. Walau bagaimana pun alator dua peringkat mempunyai dua tolok bacaan.
Terdapat dua jenis alator yang boleh digunaka dalam pemasangan oksi-
asetilina. Iaitu:
-Alator satu peringkat
-Alator dua peringkat
7.8.1 Tugas-tugas dan fungsi alator alator.
Alator satu peringkat mempunyai satu ruang tekanan tinggi dimana tekanan tinggi dari silinder terus masuk ke dalam ruang ini bacaan tekanan dapat dilihat pada jarum alator dan sedia dikurangkan kepada tekanan untuk kerja mengikut pelarasan yang sesuai dengan menggunakan skru pelaras pad alator. Tahap keselamatan alator ini adalah rendah berbanding alator dua peringkat.
Alator dua peringkat mempunyai dua ruang tekanan iaitu ruang tekanan rendah dan ruang tekanan tinggi. Ruang tekanan tinggi pada alator menerima terus tekanan tinggi dalam silinder dan bacaan bagi tekanan ini dapat dibaca pada tolok tekanan. Manakala ruang tekanan rendah menerima gas yang dikawal kemasukannya dari ruang tekanan tinggi dengan melaraskan skru pelaras pada alator mengikut tekanan kerja yang dikehendaki. Oleh itu tahap keselamatannya adalah lebih baik berbanding alator satu peringkat.
Contoh 7.3
Senaraikan campuran gas bahan bakar dan suhu kepanasanya.
Penyelesaian:
i) oksi-asetilina 3100C - 3500C
ii) udara-asetilina 2300C - 2500C
iii) oksi-hidrogen 2200C - 2382C
1v) oksi-gas arang batu 1982C - 2182C
7.9 Jenis-Jenis Hos
Hos adalah tiub getah berlapiskan benang nylon yang kuat . Ia digunakan untuk mengalirkan gas dari silinder ke sumpitan api. Tahan api dan tahan pada tekanan tinggi. Hos boleh didapati dalam rekabentuk berkembar dan juga tunggal. Namun begitu hos berkembar mempunyai cirri-ciri keselamatan yang tinggi.
7.10 Prinsip Serta Jenis Sumpitan Api
Sumpitan api kimpalan adalah alat yang digunakan untuk mengeluarkan nyalaan hasil percampuran antara gas oksigen dan asetilina didalam ruang percampuran di dalam badan sumpitan api berkenaan. Nyalaan oksi-asetilina itu dikawal oleh dua injap yang terdapat dibadan sumpitan api. Injap-injap itu ialah injap oksigen dan injap asetilina.
Saiz muncung sumpitan api boleh didapati dalam berbagai saiz dan juga rekabentuk yang berlainan. Nombor bagi saiz muncung sumpitan dicetak pada panglal muncung. Muncung sumpitan juga boleh di dapati dalam berbagai rekabentuk dan jenama.
Alat-alat penyambung adalah terdiri daripada nat-nat berbenang dalam dan juga ‘nipple’ bagi menghubungkan hos dengan alatur dan juga badan sumpitan api. Kebanyakan alat penyambung ini diperbuat daripada gangsa dan aluminium.
Contoh 7.4
Mengapakah arah bebenang oksigen dibuat berbeza dengan bebenag asetilin?
Penyelesaian:
Bebenang oksigen dan bebnang asetilina mempunyai arah yang berlainan kerana semata-mata untuk tidak tersalah demi keselamatan alat dan jurukimpal.
7.11 Badan sumpitan-api
Badan sumpitan api adalah sebahagian daripada kelengkapan dalam pemasangan oksi-asetilina. Ianya berfunsi sebagai alat untuk mencampurkan gas asetilina dan oksigen mengikut nisbah yang tertentu bagi menghasilkan jenis nyalaan yang diperlukan.
7.11.1 Jenis-jenis badan sumpitan-api.
Terdapat dua jenis badan sumpitan-api yang digunakan, Iaitu:
i.Jenis tekanan seimbang
ii. Jenis injector
Badan sumpitan api tekanan seimbang ialah dimana kedua-dua gas akan masuk dan bercampur di dalam ruang percampuran. Manakala Badan sumpitan-api tekanan tinggi dimana pengaliran oksigen pada kelajuan yang lebih tinggi akan bercampur dengan gas asetilina sebelum memasuki ruang percampuran dan ianya digunakan jika janakuasa tekanan rendah digunakan
7.12 Sistem Pancarongga Kimpalan Gas.
Sistem pancarongga adalah satu anifo pemasangan kimpalan gas dimana silinder-silinder gas oksigen dan asetilina dikumpulkan disatu tempat berasingan diantara keduanya. Penyaluran gas bagi kedua-duanya akan disalurkan melalui paip keluli ke setiap setesen kimpalan.
Bagi anifo tunggal pula silinder oksigen dan asetilina akan digandingkan bersama-sama disetiap setesen kimpalan. Tetapi cara ini mempunyai anif-ciri keselamatan yang rendah dan tidak begitu menjimatkan penggunaan gas.
Oleh itu anifo pancarongga mempunyai anif-ciri keselamatan yang tinggi serta penjimatan dalam penggunaan gas berbanding anifo tunggal. Lebih-lebih lagi apabila banyak setesen beroperasi serentak. Ruang kerja pada setiap stesen kimpalan juga akan jadi lebih luas dan selesa.
Contoh 7.5
Apakah kebaikan menggunakan system anifold dalam pemasangan kimpalan oksi-asetilina?
Penyelesaian:
Sisitem Manifol adalah system yang paling selamat dan menjimatkan gas digunakan untuk kerja kimpalan gas kerana:
- silinder-selinder oksigen dan asetilina diletakan pada tempat yang berlainan.
- System ini mempunyai sebuah alator pusat yang mengawal tekanan ke tempat kerja.
- Menjimatkan ruang tempat bekerja
- Menggunakan gas secara maksima
LOJI KUASA STIM
Pengenalan
Sebuah loji kuasa stim menggunakan tenaga haba yang dihasilkan dari pembakaran bahan api seperti minyak diesel, arang batu atau bahan-bahan lain yang boleh dibakar untuk menghasilkan tenaga elektrik. Loji jenis ini digunakan secara meluas di muka bumi.
Loji ini menggunakan kitar Rankine. Kitar ini menerangkan stim yang dihasilkan oleh dandang, kemudian dihantar ke turbin stim ( penggerak utama ). Dari turbin, stim disejukkan kembali menjadi air yang berlaku di pemelowap, menghasilkan air tersebut disuap balik ke dandang untuk mengulangi proses penghasilan stim semula.
Kerana kepelbagaian bahan api yang boleh digunakan, loji jenis ini boleh digunakan untuk menghasilkan jumlah tenaga elektrik yang lebih besar. Di kebanyakan negara, loji ini dijadikan loji muatan pengkalan. Ini kerana loji kuasa stim lambat untuk dihidupkan dan tidak boleh digunakan sebagai pembekal tenaga untuk muatan kemuncak yang umumnya berlaku pada waktu yang singkat.
Loji kuasa ini yang digunakan bersama loji kuasa nuklear dijalankan hampir kepada keupayaan sepenuhnya untuk tempoh 24 jam sehari. Loji ini mempunyai tempoh hayat dari 30-40 tahun.
Gambarajah asas operasi loji kuasa stim

LOJI TURBIN GAS
Pengenalan
Sebuah loji kuasa turbin gas menggunakan turbin gas sebagai penggerak utama untuk menghasilkan tenaga elektrik.
Loji kuasa ini secara umumnya digunakan bersama loji kuasa stim. Loji kuasa jenis ini boleh digunakan untuk menghasilkan jumlah tenaga elektrik yang terhad. Di kebanyakan negara loji kuasa ini digunakan sebagai loji kuasa kemuncak.
Operasi
Loji kuasa ini di jalankan dengan menggunakan gas asli sebagai bahan api. Turbin menyedut angin di bahagian hadapannya, kemudian memampat, bercampur dengan bahan api dan menyalakan campuran udara mampat dan gas asli pada tekanan tinggi. Gas panas yang dilepaskan mengembang melalui bilah turbin, yang dihubungkan dengan syaf turbin. Syaf bergerak seterusnya menghasilkan tenaga mekanikal yang kemudiannya ditukarkan menjadi tenaga elektrik oleh penjana.
Gambarajah asas loji turbin gas.

LOJI KUASA NUKLEAR
Pengenalan
Sebuah loji kuasa nuklear menggunakan tenaga nuklear untuk menjana tenaga elektrik.
Loji kuasa ini secara umumnya terletak jauh dari kawasan yang berpopulasi. Loji kuasa jenis ini boleh digunakan untuk menghasilkan tenaga elektrik dengan jumlah lebih besar. Di kebanyakan negara loji ini dijadikan sebagai loji kuasa muatan pengkalan. Ini kerana ia boleh mengambil masa selama beberapa hari untuk dipanaskan dan digunakan untuk operasi.
Operasi
Elemen-elemen yang berat seperti Uranium (U235) atau Thorium (Th232) adalah subjek kepada pembelahan tenaga nuklear dalam sebuah reaktor untuk menghasilkan stim bersuhu dan bertekanan tinggi.
Stim menggerakkan turbin stim yang menukarkan tenaga nuklear ini kepada tenaga mekanikal.
Turbin stim kemudiannya menjalankan pengulang-alik yang menukarkan tenaga mekanikal kepada tenaga elektrik.
Gambarajah asas operasi loji kuasa nuklear
